Huisman scales up 3D printing of crane hooks
Huisman, the worldwide provider of step changing technical solutions, has successfully tested four new 3D printed 350mt crane hooks according to the strictest criteria, and under the supervision of the independent certification authority Lloyd's Register.
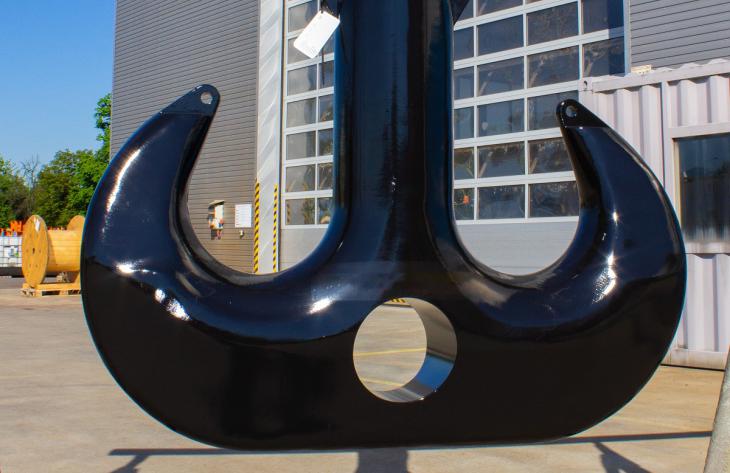
The hooks are approx. 170 by 130cm in size, almost 9 times larger than the first Huisman 3D printed crane hook. They have a weight of 1,700kg each and a loading capacity of 350mt. Each hook exists of approx. 90 kilometres of welding wire.
Huisman has been employing the 3D printing technique ‘Wire & Arc Additive Manufacturing’ (WAAM) to produce mid-size to large components with high-grade tensile steel. An important benefit of using this technique for crane hooks is the significant reduction in delivery time at a cost that competes with forgings and castings, and a more consistent quality level.
Huisman has plans to expand its robotic workplace of its production facility in Sviadnov, Czech Republic, which currently holds three welding robots. By upgrading its capacity, Huisman will be able to produce crane hooks with a weight up to 5,000 kg.
Daniel Bílek, Project Coordinator said: "Crane hooks are commonly part of the delivery of heavy lifting cranes for the offshore industry, one of our key products. The price of a forged hook increases exponentially with size, especially if it is a non-standard size. If a hook is produced by casting, the problem of inconsistent internal quality could result in longer delivery times. All this led to the idea of making the hooks ourselves, using the so-called WAAM method. After 5 years of research, development and testing of 3D printed products, we have gained the necessary expertise to use this innovative method for the production of high quality crane hooks."
Main benefits of 3D printed crane hooks:
- High control over process and material quality
- Layer-by-layer manufacturing, enabling a new range of component shapes
- Cost and/or lead time reduction for critical components
- Tailor-made material properties within same product: strength, ductility, and wear/corrosion-resistance